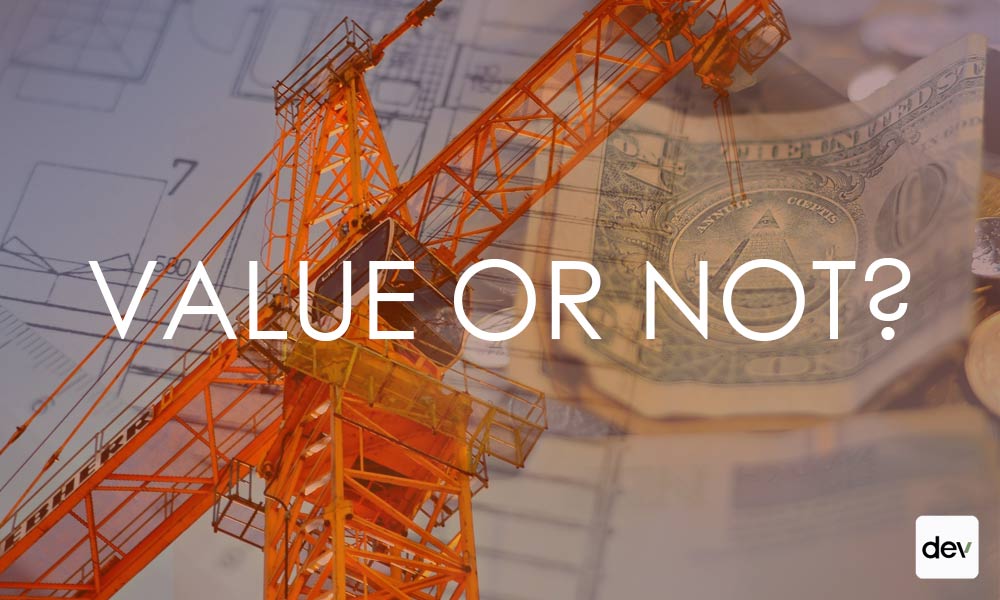
Design
Value Engineering – Get It Right Every Time
Dive into the world of value engineering to discover how it can streamline your real estate development projects. Learn how value engineering can drive practical strategies for implementing cost-effective solutions without compromising quality. Essential reading for developers aiming for maximum project value.
Commercial real estate construction is a team sport. All project partners must work toward the same goal to transform a blueprint into reality. However, balancing each team member’s costs, time commitments, and schedule is a lot more complicated than it sounds. Without a clear plan to control construction costs, a building may become unprofitable before the first crews appear on site.
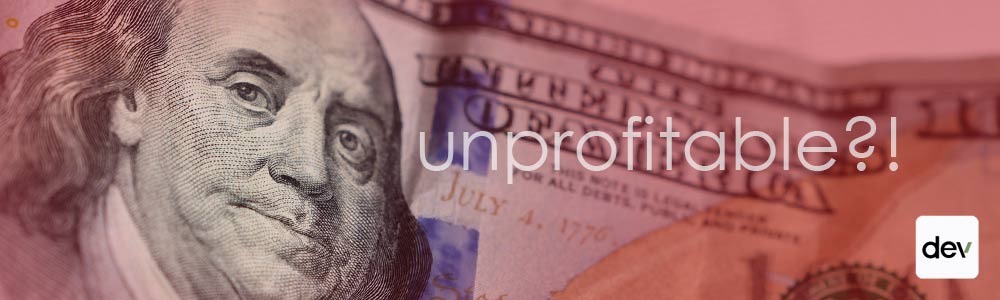
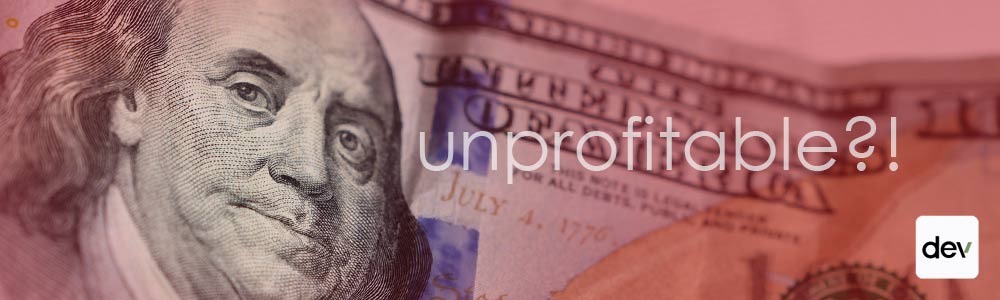
That’s where Value Engineering (VE) comes in. VE is a systematic approach to saving money on construction costs without sacrificing a development’s overall quality or value. It’s more than simply scaling back labor hours or substituting cheaper materials for more expensive ones. There are numerous ways to accomplish this, and no two methods are the same. That being said, a few principles apply in almost every VE session. Some examples include focusing on the client’s needs and documenting how the VE team came to their conclusions.
VE is beneficial not only for commercial construction projects, but also is an essential part of a building’s long-term financial success. How your team approaches VE could make or break a project. That’s why it’s vital to get it right every time. This guide will give you a few tips and tricks to help you master the art of VE.


What is the meaning of value engineering?
VE can mean different things to different project partners. Overall, it is a creative process that identifies project areas where costs can be reduced without sacrificing the overall quality of construction or the value of a development. This process can be used to analyze a project from a service, systems, or product level.
This process is about more than simply cutting costs. In the end, a successful VE solves problems. VE sessions focus on identifying alternative materials, systems, features, or equipment that reduce barriers to completing construction and provide greater value for the project. For instance, plans for a hospital may call for a switchgear system that costs more than $150,000. VE may help the project’s general contractor identify a superior product that costs less but adds more value.
VE can also be used to analyze the services or systems of an existing building. This process includes the same principles of a VE session before a building is constructed, such as elevating function over form and identifying design areas that could provide more value.
What are the five key principles of value engineering?
- Put the client’s needs first: While putting the client’s needs ahead of your own may seem simple enough, the practical implications are immense. This involves regularly communicating with and seeking feedback from your client and project partners. This process ensures that the solutions identified during the VE process align with the client’s goals, which is ultimately what decides the “value” of a project.
- Focus on function, not form: No VE session will be successful if it doesn’t focus on a building’s function. That means VE teams need to focus on the purpose of each component, not necessarily its physical form. That could mean changing out one fan box for another to improve the element’s life span, even if the new fan box is less aesthetically pleasing.
- Inspect every expense to maximize cost-benefit: Nothing is off-limits during a VE session. Every bolt and screw included in the plans needs to have an identifiable benefit to the long-term viability of a construction project. The same is true for the functionality of a building. VE teams need to enter a session with a certain cost-benefit threshold in mind and cut out any aspect that does not meet that criteria.
- Teamwork makes the dream work: VE is a multidisciplinary approach that includes the perspectives of engineering, architecture, finance, and manufacturing professionals. This approach is critical for comprehensive problem-solving, but the diversity of perspectives can also make VE sessions difficult to manage effectively. Maintaining open lines of communication is crucial, and the practice of disparaging ideas should not be welcomed during these sessions. Make sure every partner is a good teammate.
- Document everything: VE demands thorough documentation about the team’s analyses, decisions, and methodologies. These notes can be invaluable for a project’s long-term success as they allow future operators to see how the team came to its conclusions. These documents can also guide future decisions about how to improve the efficiency or value of a building.
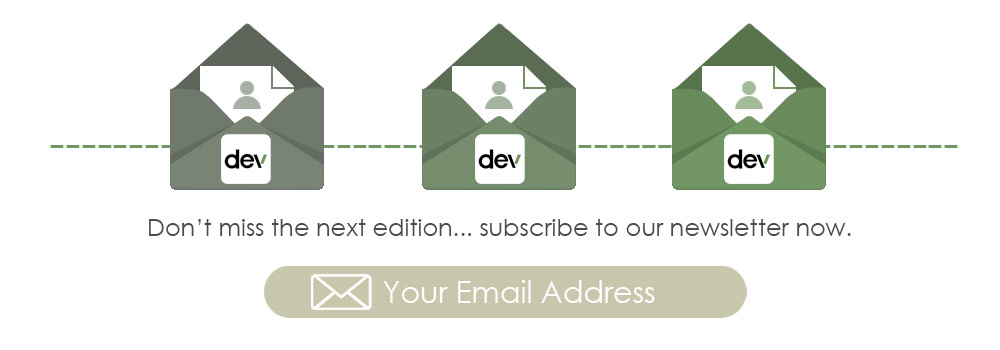
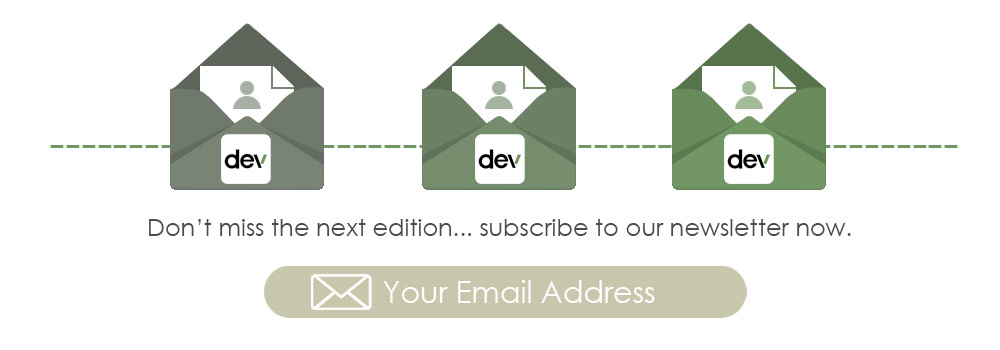
What is a good example of value engineering?
A recent example of how VE can impact a project is the Portland International Airport’s main terminal upgrade. The project, which local architecture firm ZGF designed, aims to add more than 2.6 million board feet of glulam beams and another 400,000 board feet of mass plywood panels to create an oasis-like terminal out of mass timber products.
Given that the project is located in the Pacific Northwest, ZGF and its project partners had plenty of mass timber products to choose from. The designers ultimately settled on glulam beams made from Douglas fir trees within 300 miles of the property. The Douglas fir glulam beams cost about half as much as those made from spruce trees, which are also common in the PNW area. Wood from Douglas firs is also stronger compared to spruce wood, thereby increasing the life of the finished product.
What is the aim of value engineering?
Value engineering aims to reduce life-cycle costs by minimizing the cost of construction and improving the overall functionality or quality of the building. While laborious, this process can also create significant competitive advantages for firms that master the art of VE. Teams that do VE well often have more efficient construction processes and are better at managing risk and innovating new construction methodologies. This makes VE a valuable tool that every firm should use.
There are downsides to VE that firms need to be aware of. For instance, VE processes are limited in scope. While they can identify issues with materials or construction, VE often overlooks broader organizational issues that can impact a project’s timeline. VE processes also require specialized knowledge and skills that can be difficult to source. Managing these risks is vital to maximizing the return on investment for VE sessions.
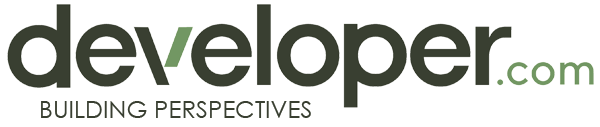
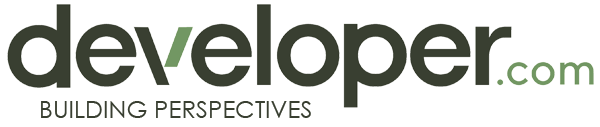